Digital transformation is revolutionizing the cement industry by integrating advanced digital technologies into all areas of operations. This shift aims to enhance process control, improve product quality, reduce downtime, and optimize logistics and supply chain management. With real-time data analysis, predictive maintenance, and automated control systems, cement plants can significantly boost their operational efficiency and sustainability. This article explores the key areas where digital transformation can make a substantial impact on cement manufacturing.
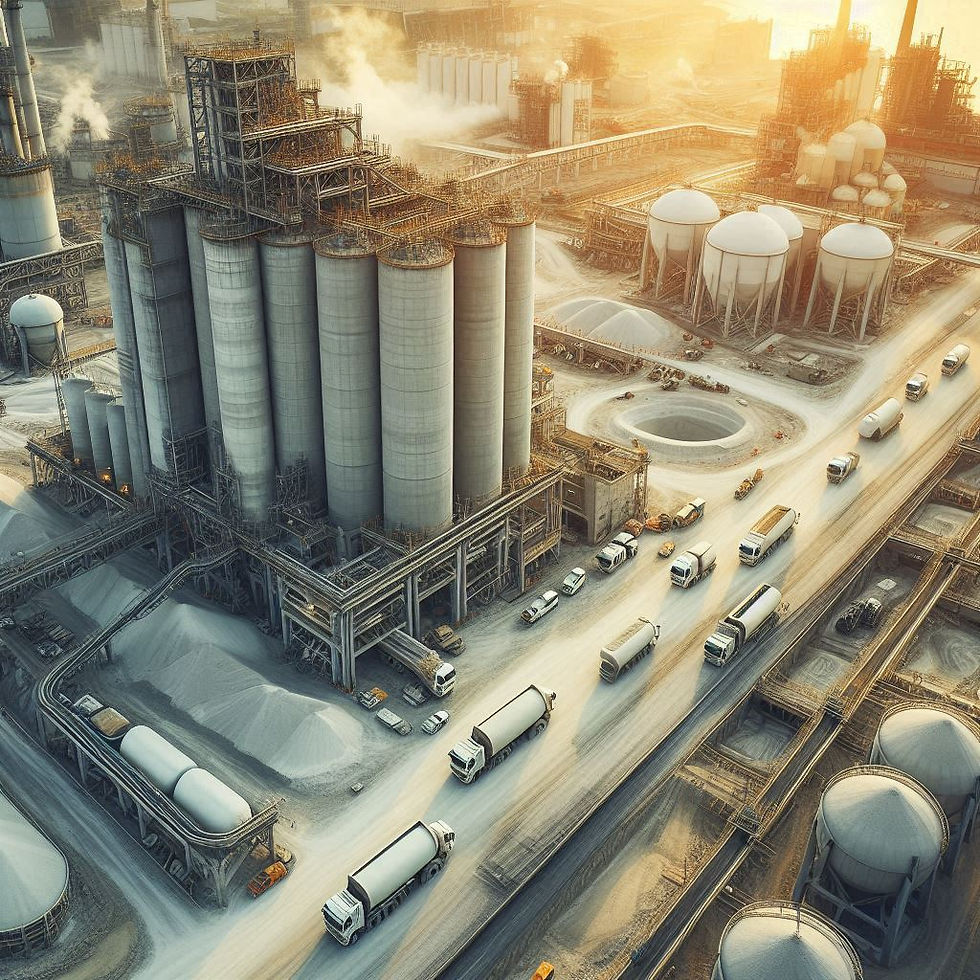
Key Takeaways
Real-time data integration and advanced analytics are crucial for enhancing process control in cement plants.
Digital solutions can significantly improve product quality through quality monitoring tools and predictive quality control.
Predictive maintenance and remote monitoring systems help in reducing downtime and increasing asset productivity.
Optimizing logistics and supply chain management with digital platforms leads to better inventory tracking and demand forecasting.
Embracing digital transformation promotes sustainable practices by reducing carbon footprint and improving resource management.
Enhancing Process Control in Cement Plants
Real-Time Data Integration
Real-time data integration is crucial for enhancing cement output. By integrating data from various sources, cement plants can achieve a holistic view of their operations. This enables operators to make informed decisions quickly, improving overall efficiency and productivity.
Advanced Process Analytics
Advanced process analytics leverages data to optimize the clinkering process. By utilizing artificial intelligence and machine learning algorithms, plants can predict and mitigate potential issues before they arise. This proactive approach not only enhances process control but also contributes to reducing greenhouse gas emissions.
Automated Control Systems
Automated control systems are essential for maintaining consistent quality and operational efficiency. These systems can automatically adjust parameters to ensure optimal performance, reducing the need for manual intervention. This leads to more efficient and productive cement manufacturing processes.
Implementing these digital solutions can significantly improve process control in cement plants, leading to better performance and sustainability.
Improving Product Quality through Digital Solutions
Quality Monitoring Tools
Quality monitoring tools are essential in ensuring that cement plants maintain high standards. These tools provide real-time data on various quality parameters, allowing for immediate adjustments and improvements. Integrating these tools into the production process helps in identifying defects early and reducing waste.
Data-Driven Quality Adjustments
Data-driven quality adjustments leverage advanced analytics to fine-tune production processes. By analyzing data from various stages of production, plants can make informed decisions that enhance product quality. This approach not only improves the final product but also optimizes resource usage and reduces operational costs.
Predictive Quality Control
Predictive quality control uses machine learning algorithms to forecast potential quality issues before they occur. This proactive approach enables cement plants to address problems in advance, ensuring consistent product quality.
Predictive quality control bridges the gap between process and product quality control, leading to superior customer satisfaction.
By adopting these digital solutions, cement plants can significantly improve their product quality, leading to better customer satisfaction and competitive advantage.
Reducing Downtime with Predictive Maintenance
Predictive maintenance is a game-changer for cement plants, enabling them to prevent unplanned downtime by identifying potential issues before they escalate. This approach allows ample time for proactive maintenance, minimizing unexpected shutdowns and ensuring continuous operations.
Remote Monitoring Systems
Remote monitoring systems play a crucial role in predictive maintenance. By continuously tracking the operating conditions of machines and equipment, these systems can predict wear, mechanical part failures, and the timing of potential failures. This real-time data collection and analysis help in detecting critical machine behavior and malfunctions before they lead to major problems.
Predictive Analytics for Maintenance
Predictive analytics leverages comprehensive machine know-how and analytic algorithms to provide insights into the service life and health of machinery. By analyzing process and sensor data, cement plants can transition from periodic maintenance to predictive maintenance, enhancing their ability to forecast and address issues proactively.
Minimizing Unplanned Downtime
Preventive maintenance is essential for minimizing the number of unplanned plant shutdowns. By solving problems before they happen, cement plants can significantly reduce the length and impact of shutdowns. This not only improves cost-effectiveness but also ensures smoother and more efficient plant operations.
The digitalization of planning, scheduling, and monitoring using the latest technologies is key to overcoming barriers to digital adoption in the cement industry, including legacy systems and cultural resistance.
Optimizing Logistics and Supply Chain Management
Digital Supply Chain Platforms
Implementing e2e supply chain solutions can significantly enhance the efficiency of cement plants. These platforms integrate various logistical processes, from order assignment to vehicle tracking, ensuring seamless operations. By leveraging advanced logistical concepts, organizations can optimize transportation activities, reducing both economic and environmental impacts.
Real-Time Inventory Tracking
Real-time GPS tracking allows cement manufacturers to optimize delivery routes and gauge driver productivity. This not only cuts freight costs but also ensures timely deliveries. Additionally, real-time inventory tracking helps in managing inventory and adjusting the supply versus demand ratio to optimize costs.
Demand Forecasting and Planning
With accurate forecasting, it's possible to manage inventory effectively and prepare enough raw materials for production. This ensures that the right product mix is maintained, consuming the least number of resources and producing less waste. Such measures make it easier to budget accurately and meet market demand without compromising quality.
Implementing these digital solutions in logistics and supply chain management can drive significant improvements in production efficiency and cost optimization for cement plants.
Boosting Operational Efficiency with Technology
Energy Consumption Monitoring
Technology also gives cement manufacturers the ability to understand plant operations, track all activities, and spot processes optimized to improve the overall operational efficiency. For example, analyzing the fuel mix ratio to the raw material mix helps improve production rates without too much wastage. Real-time alerts on machine performance notify technicians about potential issues before they become severe and lead to costly downtime.
OEE Tracking and Improvement
Manufacturing companies started to invest in new digital technologies such as AI to improve operational efficiency in areas such as demand forecasting, fault finding in production, and warehousing. By integrating logistics operations, leveraging technology can significantly enhance overall equipment effectiveness (OEE).
Waste Reduction Strategies
Operational efficiency can be further boosted by implementing waste reduction strategies. These strategies rely on different basic concepts and elements, which must be assessed and investigated to provide a reliable background. For instance, real-time data integration and advanced process analytics can help identify areas where waste can be minimized, thus promoting sustainability in the manufacturing sector.
Overall, these technological advancements are bolstering competitiveness, enhancing customer satisfaction, and promoting sustainability in the manufacturing sector.
Overcoming Barriers to Digital Adoption
Digital transformation in cement plants is essential for improving production and efficiency. However, several barriers can impede this transformation. Addressing these barriers is crucial for a successful digital adoption strategy.
Sustainable Practices through Digital Transformation
Reducing Carbon Footprint
Digital transformation in cement plants plays a crucial role in reducing the carbon footprint. By integrating advanced data analytics and real-time monitoring, plants can optimize their energy consumption and minimize emissions. This not only helps in achieving sustainability goals but also enhances operational efficiency.
Sustainable Resource Management
Effective resource management is essential for sustainable operations. Digital tools enable cement plants to monitor resource usage accurately and make data-driven decisions to reduce waste. This includes the efficient use of raw materials and water, contributing to overall sustainability.
Compliance and Reporting
Digital solutions simplify compliance with environmental regulations by automating data collection and reporting processes. This ensures that cement plants can easily adhere to legal requirements and maintain transparency in their operations.
The digital transformation of cement manufacturing is revolutionising the industry, driving operational efficiency, sustainability, and competitiveness.
Conclusion
Digital transformation in the cement industry is not just a trend but a necessity for staying competitive and achieving operational excellence. By leveraging advanced technologies such as real-time data analysis, predictive maintenance, and intelligent plant monitoring, cement manufacturers can significantly improve their production efficiency and overall equipment effectiveness (OEE). These digital tools enable better process control, enhanced product quality, and reduced downtime, leading to substantial cost savings and more sustainable operations. As the industry continues to evolve, embracing digital transformation will be crucial for cement plants to overcome legacy system challenges and cultural resistance, ultimately driving profitability and long-term success.
Frequently Asked Questions
What is digital transformation in the cement industry?
Digital transformation in the cement industry involves integrating digital technology into all areas of the business to improve process control, product quality, availability, and reduce downtime. This includes the use of advanced data analytics, remote monitoring, and predictive maintenance systems.
How does real-time data integration benefit cement plants?
Real-time data integration allows cement manufacturers to gain complete visibility into plant operations, set up alerts for productivity drops, perform predictive maintenance, and adjust production capacity based on market demand. This helps in reducing wastage, cutting costs, improving OEE, and operating more sustainably.
What are the main objectives of digital transformation for cement producers?
The main objectives include improving process control, enhancing product quality, better availability and reduced downtime, advanced logistical concepts, and intelligent plant monitoring.
How can predictive maintenance reduce downtime in cement plants?
Predictive maintenance uses remote monitoring systems and predictive analytics to identify potential issues before they become severe. This minimizes unplanned downtime and increases asset productivity by allowing timely maintenance and repairs.
What role does data play in improving operational efficiency in cement plants?
Data provides management with crucial information for accurate business planning and budgeting. It helps track and measure KPIs such as energy consumption, OEE, and production rate, leading to improved operational efficiency by optimizing processes and reducing wastage.
What are the challenges in adopting digital technologies in the cement industry?
Challenges include addressing legacy systems, managing cultural change, and ensuring proper training and skill development for employees to effectively use new digital tools and technologies.
Commentaires